1 引言
煤化工是一個包含大量高新技術(shù)的行業(yè),保證了中國經(jīng)濟(jì)的可持續(xù)發(fā)展和能源安全。煤化工關(guān)鍵控制閥是煤化工的核心技術(shù)環(huán)節(jié)。制約煤化工關(guān)鍵控制閥長期運(yùn)行的主要因素是煤化工惡劣復(fù)雜運(yùn)行條件下閥門與流體接觸造成的磨損問題。煤化工磨損的原因復(fù)雜,主要包括固液兩相流的流速和粘度對管道磨損、外部條件和閥門結(jié)構(gòu)設(shè)計(jì)的影響。
2 國內(nèi)外研究現(xiàn)狀
2.1 國內(nèi)研究現(xiàn)狀
我國煤化工關(guān)鍵控制閥行業(yè)起步較晚,特別是高參數(shù)煤化工關(guān)鍵控制閥,其整體技術(shù)水平相當(dāng)于20世紀(jì)90年代末的國際水平,仍落后于國際先進(jìn)水平,不能滿足國內(nèi)外市場的需求。從技術(shù)分析來看,主要表現(xiàn)在以下方面:1)性能不穩(wěn)定,不符合市場發(fā)展要求,如抗壓差低、調(diào)節(jié)精度低、智能水平低、使用壽命短(耐沖刷性低);2)高參數(shù)條件,如高溫、高壓差、腐蝕強(qiáng)、磨損強(qiáng)等,控制閥難以滿足使用要求;3)缺乏有效的組織和手段效的組織和手段;4)缺乏應(yīng)用于特殊條件的材料研究和應(yīng)用;5)滿足特殊結(jié)構(gòu)設(shè)計(jì)需對落后。由于一些大型、高參數(shù)、智能、復(fù)雜的煤化工關(guān)鍵控制閥仍受人控制,煤化工關(guān)鍵控制閥技術(shù)已成為現(xiàn)代工業(yè)設(shè)備系統(tǒng)集成的主要瓶頸。
2.2 國外研究現(xiàn)狀
國外對耐磨性的機(jī)理和實(shí)驗(yàn)研究比較全面。J.Ahn通過微結(jié)構(gòu)分析和磨損試驗(yàn),增加磨損負(fù)荷會提高涂層的磨損率,硬度是耐磨性最關(guān)鍵的因素,內(nèi)部微因素(微裂紋、形狀等)和外部因素(負(fù)載、溫度等)起著重要作用。正是由于這些因素的存在,雖然有些涂層硬度較高,但磨損率高于一些硬度較低的材料。由于涂層顆粒受載荷的影響,相對硬的材料容易破裂,導(dǎo)致涂層顆粒之間的裂縫缺陷,從而影響涂層的耐磨性。
M.Yandouzi提出增加顆粒的沖擊速度和溫度可以顯著提高涂層的密度和硬度,但應(yīng)注意碳化物對溫度的敏感性。當(dāng)溫度高于一定值時,碳化物的性能開始衰減。因此,應(yīng)盡量控制顆粒溫度,使其低于衰減溫度,減少顆粒的生長。R.C.TuckerJr.采用不同的噴涂方法WC-Co表面噴涂材料,結(jié)果發(fā)現(xiàn)使用HVOF該方法生成的涂層的耐磨性遠(yuǎn)遠(yuǎn)大于等離子噴涂的耐磨性。通過試驗(yàn)發(fā)現(xiàn),粒子的速度是研究耐磨性的關(guān)鍵因素。隨著速度的提高,粒子碰撞可以產(chǎn)生良好的物理組合和致密性,這對涂層的耐磨性非常重要。
M.Richert在R.C.TuckerJr.分析了涂層晶粒的特性,認(rèn)為晶粒致密性是耐磨性的重要因素。
針對國內(nèi)煤化工閥耐磨涂料研究中存在的技術(shù)經(jīng)驗(yàn)等不足問題,本文結(jié)合國外研究成果,研究了幾種不同的工藝處理方法,采用適當(dāng)?shù)墓に囂幚矸椒ǎ鉀Q了國內(nèi)煤化工閥耐磨性問題。
3 煤化工特殊工況及典型表面處理工藝
3.1 煤化工特殊工況
煤化工閥控介質(zhì)具有以下特點(diǎn):
1)介質(zhì)溫度高,輸送溫度200~500℃;
2)介質(zhì)固體顆粒硬度高,多為HRC60左右;
3)壓差大,最高可達(dá)19MPa;
4)煤含硫,腐蝕性強(qiáng);
5)同時存在固、液、氣三相流。
一般金屬不能同時滿足耐沖刷、耐高溫、耐腐蝕的要求。碳化鎢和陶瓷雖然硬度高,但強(qiáng)度不夠,在控制閥的應(yīng)用中經(jīng)常會開裂和損壞。目前,大多數(shù)奧氏體不銹鋼硼滲透層的有效厚度只能達(dá)到10μm下面。因此,對煤化工閥的耐磨涂層研究是一種實(shí)用可行的方法。
3.2 3種典型的煤化工表面處理工藝
金屬表面的熱處理工藝很多,但針對煤化工的特殊工況,主要采用以下典型的處理工藝。
3.2.1 等離子噴涂(APS)
等離子噴涂(APS)過程是利用高壓電弧加熱氣流,產(chǎn)生高速等離子體射流。等離子體產(chǎn)生的氣體通常是含有少量氫或氦的氬氣,從而有效地加熱和熔化輸送的粉末。等離子體弧的溫度通常高于1萬K,粒子沖擊速度高達(dá)250m/s。APS原理如圖1所示。
圖1
3.2.2 超音速火焰噴涂(HVOF)
超超音速火焰噴涂過程中,燃料和氧氣在燃燒室內(nèi)被壓制、點(diǎn)燃,并通過擴(kuò)展音速噴嘴加速到超音速,形成馬赫錐。最后,顆粒在高速(>400m/s)溫度相對較低(2000℃)同時,軸向進(jìn)粉,以提供更均勻的加熱顆粒。HVOF由于低氧化性和高速顆粒的沖擊,噴涂通常不需要后續(xù)的熱處理,從而形成致密、結(jié)實(shí)的噴涂層。HVOF原理如圖2所示。
圖2
3.2.3 等離子堆焊(PTA)
PTA焊接工藝及氬弧焊(tungsteminsertgasTIG)過程相似。電弧受噴嘴和保護(hù)氣體的限制,產(chǎn)生收縮柱弧。噴粉主要是合金和碳化物,通過載體離子氣加入溫度穩(wěn)定的柱弧。同時,均勻分布的環(huán)保氣體可以保護(hù)焊接區(qū)域不暴露在空氣中,減少和防止氧化。在堆焊技術(shù)中,PTA基層堆積層的稀釋率相對較低,保持了堆積層的化學(xué)特性,最大限度地減少了噴涂部件熱影響區(qū)的融深。PTA原理如圖3所示。
圖3
♂
3.3 試驗(yàn)涂層粉末,工藝參數(shù)
根據(jù)上述三種典型工藝,在試驗(yàn)過程中使用了多種適合煤化工條件的粉末材料,其中APS選擇Ni-Cr-B-Si等自熔合金粉末的結(jié)晶溫度為1萬℃大約。噴涂層堆積在950~1100℃加熱并部分熔化。合金粉末中高濃度Si防止基體表面和噴涂層在加熱過程中氧化。由于涂層被加熱并部分熔化,基體和涂層的結(jié)合力增加。
針對HVOF本實(shí)驗(yàn)選用含85%的工藝WC鈷鉻合金粉(WY-M516)。這些粉末主要用于耐磨和耐腐蝕。鉻提高了耐腐蝕性,優(yōu)良的硬合金顆粒提高了碳化物鈷基材料的耐腐蝕性和磨損性。
PTA一般選用堆焊粉WC含60%以上的粉末和含60%以上的粉末Ni-17Cr-Fe-B-Si的合金粉末(WY-SY64)。
綜合以上分析,選擇不同的粉末材料,具體性能特點(diǎn)及應(yīng)用如表1所示。
表1 噴涂粉末選擇
測試樣品的尺寸為25mm×80mm×6mm的410不銹鋼。
選擇等離子噴涂SG-不同粉末的噴涂參數(shù)保持不變,如表2所示,噴涂層厚度為0.4~0.6mm。
表2
HVOF用DJ2700噴槍,鈷基碳化鎢噴涂,丙烯燃料噴涂參數(shù)如表3所示,樣品噴涂厚度為0.4mm。
表3 超聲噴涂參數(shù)
PTA堆焊參數(shù)如表4所示,堆焊層厚4mm。
表4
3.4 樣品試驗(yàn)方法及結(jié)果分析
3.4.1測試方法
磨粒磨損的主要特點(diǎn):1)磨粒磨損屬于三維磨粒磨損形式,類似于實(shí)際工況;2)磨粒磨損的可控參數(shù)較少。雖然不能完全模擬實(shí)際工況的參數(shù),但操作簡單,可重復(fù)性高,可靠性好。因此,在試驗(yàn)階段對樣品進(jìn)行磨損試驗(yàn)。
磨損試驗(yàn)一致ASTM-G-65-85。根據(jù)這個技術(shù)標(biāo)準(zhǔn),樣品放于橡膠輪一邊,同時向它們之間注入磨料,對磨料的流速進(jìn)行控制,示意圖和實(shí)物圖如圖4所示。設(shè)置循環(huán)次數(shù)為2000次,另一側(cè)加載30磅的載荷進(jìn)行實(shí)驗(yàn)測試(標(biāo)準(zhǔn)G-65測試的B程序)。樣品磨損前后的質(zhì)量磨損量由直接稱重測量,精度為0.001g。在測試前,PTA堆焊樣品加工成平面。
圖4 磨損試驗(yàn)機(jī)
3.4.2 測試結(jié)果分析
圖5 噴涂樣品(從左到右)HVOF、APS、PTA
圖5顯示了三種工藝樣品,其中HVOF涂層表面致密,APS樣品表面相對松動,PTA樣品結(jié)晶顯示出細(xì)密的堆焊條紋和金屬光澤。
♂
微硬度測試得出結(jié)論HVOF涂層的(WY-M516)硬度是HV=1097,PTA堆焊的硬度是HRC=60.4。
圖6顯示了各種樣品磨損試驗(yàn)后的磨損痕跡。從樣品中可以看出,磨損痕跡的大小不僅取決于工藝方法,還取決于噴涂材料。表5是各種樣品磨損量的試驗(yàn)結(jié)果。
圖6 磨損擦痕試驗(yàn)G-65
表5 磨損試驗(yàn)結(jié)果(1)(2000轉(zhuǎn))
從表6可以看出,APS涂層耐顆粒磨損的綜合性能略低于HVOF和PTA,原因是:APS粉粒的沖擊速度為250m/s,顆粒之間的機(jī)械結(jié)合強(qiáng)度遠(yuǎn)小于HVOF(400~800m/s)該工藝決定了涂層的致密性低于HVOF和PTA。
APS工藝中心弧的溫度高達(dá)1萬℃,高溫對顆粒特別是硬質(zhì)相有一定的破壞作用WC表面顆粒雜質(zhì)分解增多。
APS工藝中,WC與顆粒磨損相比,硬質(zhì)起著雙重作用。一方面,因?yàn)閃C涂層中的存在WC與抗流體相比,顆粒的硬度增加了沖擊磨損能力;另一方面,由于顆粒的硬度WC與周圍熔融相的結(jié)合缺陷可能會導(dǎo)致WC相的整體脫落破壞了APS涂層。在腐蝕磨損中,涂層的破壞機(jī)制隨著沖刷角度的不同而不同。垂直沖刷往往會導(dǎo)致沖刷點(diǎn)脈動的微疲勞變形,導(dǎo)致涂層脫落。傾斜沖刷是一種側(cè)微切割和犁,相對較軟的基底材料被侵蝕,然后硬相暴露,逐漸與基底產(chǎn)生疲勞應(yīng)力損傷,最終使整個涂層脫落。
表6 磨損試驗(yàn)結(jié)果(2)(2000轉(zhuǎn))
基于上述情況,為了提高顆粒間的結(jié)合強(qiáng)度,一般采用APS 熔敷處理工藝。
從表6可以看出,樣品的磨損量明顯低于單APS樣品3處理涂層F和4F耐磨性遠(yuǎn)高于樣品3和4,因?yàn)槿刍^程中形成的共晶組織對噴涂層起到固溶強(qiáng)化和彌散強(qiáng)化的作用WC硬合金相的組合力;涂層之間的合金相互擴(kuò)散,增強(qiáng)了涂層的韌性,提高了樣品的耐磨性。另一方面,為了提高耐磨性,硬質(zhì)階段可以直接取消,噴涂粉末可以選擇整體耐磨、無明顯內(nèi)部組合缺陷的材料,如樣品6F。
如表7所示HVOF該工藝可產(chǎn)生致密的噴涂層,通過HVOF噴涂樣品2磨損率小,尤其是樣品5最小。
表7 磨損試驗(yàn)結(jié)果(3)(2000轉(zhuǎn))
PTA涂層更耐磨,因?yàn)榻饘倩w在噴涂過程中完全熔化,并與硬相結(jié)合。當(dāng)然,金屬基體與硬相之間的巨大物理差異對其可容納的硬相的能力有很大的限制。金屬相的組合能力越強(qiáng),其抗顆粒磨損能力就越差。其綜合效果往往會導(dǎo)致PTA涂層的耐磨性介于APS和HVOF但是因?yàn)镻TA熔池冶金擴(kuò)散過程可形成金屬結(jié)構(gòu)較均勻的厚壁涂層,綜合耐磨性很好。
3.4.3 樣品微觀結(jié)構(gòu)研究
在電子顯微鏡下,對噴涂層的微觀結(jié)構(gòu)進(jìn)行了分析。F等離子噴涂和熔噴涂和熔融涂層35%WC鎳基自熔合金具有較高的共晶組織韌性和較高的等離子體噴涂溫度,導(dǎo)致碳化物氧化并溶解在基體中。典型的層狀形態(tài)觀察到等離子體沉積層,明亮的部分是合金WC-Co顆粒。在高倍顯微鏡下可高倍顯微鏡下看到。WC顆粒(見圖7)。
圖7 APS樣件1F(溶敷)
3F號和4F樣品的等離子噴涂沉積層含有WC微觀結(jié)構(gòu)圖中顯示的自熔合金粉末相對較大顆粒WC顆粒(見圖8),WC與周圍合金形成共晶組織,加強(qiáng)WC硬質(zhì)相的結(jié)合力提高了樣品的耐磨性。
圖8 APS樣件3F(左圖,熔敷)
4F(右圖,溶敷)
♂
樣品6F(見圖9)是Ni-17合金,無其他硬合金階段。該結(jié)構(gòu)相對致密,有少量圓孔,涂層與基體表面緊密結(jié)合。它的耐磨性高于使用WC顆粒等離子噴涂涂層。
圖9 APS樣件6F(熔敷)
和APS噴涂不同,HVOF在熱噴涂過程中,粒子的沖擊速度高達(dá)800m/s,無過熱現(xiàn)象,涂層壓力應(yīng)力高,密度高,涂層孔隙率低于2%,因此樣品2和5的表面致密,無孔和分層。
從圖10和圖11可以看出,樣品2涂層的微觀結(jié)構(gòu)有兩層,即金屬基體和WC顆粒;樣品5的噴涂層也相似WC晶粒分布。樣品5可以在相同的放大比例下看到WC顆粒比樣品2小,密度大,孔隙率小,所以樣品5的耐磨性高于樣品2。
圖10 HVOF樣件2(WC-12Co)不同分辨率下的微觀結(jié)構(gòu)
圖11 HVOF樣件5(WC-10Co)微同分辨率下的微結(jié)構(gòu)
PTA堆焊層很大WC這些顆粒在整個堆焊層中分布不均勻,亮部分),在整個堆焊層中分布不均勻;同時PTA堆焊時溫度比較高,WC分解形成新物質(zhì)W2C,W2C比WC脆,降低涂層的耐磨性;但從圖中可以看出,WC顆粒在涂層表面附近浮動WC分布密集,WC復(fù)合相化合物與合金元素形成,增強(qiáng)耐磨性。
圖12 PTA樣件7(40%WC-Ni-Cr-B)表面區(qū)域和涂層基體界面的微觀結(jié)構(gòu)
4 工程應(yīng)用
根據(jù)上述不同表面處理方法的特點(diǎn),選擇不同的工況和零件要求。
4.1 PTA焊接偏心旋轉(zhuǎn)閥體內(nèi)腔體內(nèi)腔體
PTA堆焊主要用于處理型面簡單的零件表面和內(nèi)壁。保護(hù)表面需要一定的涂層厚度、耐腐蝕性和耐磨性。偏心旋轉(zhuǎn)閥體內(nèi)腔用于煤化工灰水處理PTA樣品7(40%)WC-Ni-Cr-B),堆焊層厚度可達(dá)2mm。閥門的使用條件為:灰渣量占介質(zhì)總量的3%~5%,介質(zhì)溫度為250℃,介質(zhì)流量可達(dá)35m/s。經(jīng)過PTA處理后,閥門在現(xiàn)場使用良好。據(jù)制造商介紹,過去使用的非非非PTA噴涂過程中處理的閥體內(nèi)腔只能在20天以上的時間內(nèi)沖洗損壞?,F(xiàn)在使用2個多月后,閥體沖洗如圖13所示,沒有明顯的損壞痕跡。
圖13 PTA堆焊閥體內(nèi)腔使用后效果好
4.2 HVOF閥芯噴涂鎖渣閥
煤化工條件下使用的鎖渣閥需要高硬度、高耐磨性。因此,鎖渣閥的閥芯采用HVOF噴涂后表面硬度可達(dá)到表面處理工藝HV1100(見圖14)。閥門的使用條件為:介質(zhì)溫度270℃,排渣量1057kg/h,灰渣占介質(zhì)總量的50%,粒度為3~50mm。選材采用WY-M516(WC-10Co4Cr),要求配合面硬度高,適應(yīng)溫度突然變化,涂層結(jié)合力強(qiáng)。目前,該產(chǎn)品的性能測試已經(jīng)完成,并已被國內(nèi)一個煤化工項(xiàng)目用于替代國外產(chǎn)品。
圖14 HVOF噴涂后的球芯
4.3 噴涂加熔敷偏心旋轉(zhuǎn)閥閥體閥芯
由于普通噴涂表面附著力差,為了提高附著力,應(yīng)進(jìn)行第二步熔化處理,增加材料與基體的結(jié)合力,使涂層在使用過程中不會剝落。表面使用WY-W77合金(40WC-Ni-17Cr)。用于煤化工灰水處理工況,由于工況極差、高溫、高腐蝕,閥芯在使用20天后被沖刷損壞。但在現(xiàn)有工藝條件下,與其他工藝相比,使用壽命提高了3倍以上,如圖15所示,噴涂熔化處理閥芯使用6個月后損壞。
圖15 熔敷閥芯
5 結(jié)論
本文主要研究APS、HVOF和PTA三種表面熱噴涂方法的噴涂機(jī)理,采用廠家推薦的控制參數(shù)和粉末制備樣品,觀察和分析涂層性能,并根據(jù)三種不同的工藝特點(diǎn)應(yīng)用于煤化工閥門。本文的研究為煤化工閥門的發(fā)展提供了技術(shù)支持。
通過實(shí)驗(yàn)研究得出以下結(jié)論:
1)噴涂層的密度,金屬的氧化,WC影響涂層耐磨性的關(guān)鍵因素是顆粒的大小、分布和間距;
2)等離子噴涂后熔化,形成共晶組織,對噴涂層起到固溶強(qiáng)化和彌散強(qiáng)化的作用WC硬質(zhì)合金相的結(jié)合力提高了耐磨性;
3)HVOF噴射速度大,加工溫度低,金相組織保留完好,WC含量高、致密、孔隙率低、涂層薄,適用于硬密封球芯;
4)PTA堆焊的涂層和基體的結(jié)合力較強(qiáng),WC與合金元素形成塊狀硬相,使涂層硬度高,耐磨性介于APS和HVOF涂層厚度大,適用于處理閥座、閥體內(nèi)腔等;
5)將不同的表面處理工藝應(yīng)用于不同的工況和零件,改進(jìn)效果非常顯著;
6)部分工況極其惡劣,必須進(jìn)一步開發(fā)新的噴涂材料和工藝。
下一步的研究將考慮通過正交試驗(yàn)、回歸分析等方法優(yōu)化三種表面熱噴涂工藝的參數(shù),并找出影響規(guī)律的主要因素。
咨詢需求
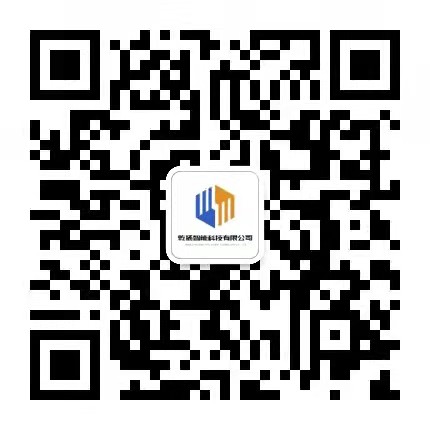